Hazard Communication Manual |
![]() |
HAZARD COMMUNICATION MANUAL
U. S. PLANT, SOIL, & NUTRITION LABORATORY ITHACA, NY
Unites States Department of Agriculture
Agricultural Research Service
Prepared by: Kathie Moh, 2002
Stephen Schaefer, 1999
Environmental Protection Specialist
USDA/ARS/NAA
TABLE OF CONTENT
- Safety Personnel Introduction/ Who to Call
- Emergency Evacuation Plan
- Emergency Response Plan
- Emergency Equipment
- Laboratory Safety
- Chemical Waste Handling & Disposal Procedures
- Personal Protection Equipment
- Summary of Lab Safety
- Radiation Safety
- Farm/Research Plot Safety
- Defensive Driving
- Office Safety
- Safety Training Requirements
- New Employee Safety Orientation
- Student Employee Policy
- Appendix B: Response to Moderately or High-Level Hazard Spill
- Appendix C: Identification, Handling, Storage and Disposal Of Chemical Waste and Excess
- Appendix D: Required Laboratory Hazard Assessment Survey OSHA 29 CFR 1910.132-138
- Appendix E: Hand Protection and Glove Selection for Specific Chemicals
- Appendix F: Standard Operating Procedures for Pesticide Application
- Appendix G: New Employee Safety Training Requirement Survey
- Appendix H: Employee Safety Training Requirement
- Appendix I: Employee Safety Checklist
U. S. Plant, Soil, & Nutrition Laboratory Safety Committee
- Kathie Moh, Environmental Protection Specialist / Safety Officer, 255-8849, Room G45
- Bill Armstrong, Facilities Coordinator, 254-9739, Room G35
- Ray Glahn, Radiation Protection Officer / Research Physiologist 255-2452, Room 203
- Mary Bodis, Lab Manager, 255-0665, Room 206
- Mark Ramos, Entomologist, 255-0496, Room 331
North Atlantic Area Safety, Health, & Environmental Management Personnel
- Bonnie DiSalvo, Area Safety & Health Manager, (215) 233-6592
- Kathie Moh, Environmental Protection Specialist, Northern Cluster, 255-8849
- Glen Davis, Environmental Protection Specialist, Southern Cluster, (304) 725-3451 X309
Cornell University Environmental Health & Safety Personnel
- Andy Garcia-Rivera, Director, 255-4125
- Ted Murray, Fire Protection & Emergency Services Manager, 254-1633
- Jim Grieger, Occupational Health & Safety Manager, 255-5615
- Tom McGiff, Laboratory & Radiation Safety Manager, 255-5835
- Allan Dye, Chemical Hygiene Officer, 255-4288
- Mary-Lynn Cummings, Assistant Director of Occupational & Environmental Health, CALS, 255-2557
USPSNL EMERGENCY NUMBER: 911
INTRODUCTION
The U. S. Plant, Soil, & Nutrition Laboratory (USPSNL) seriously cares about the safety of employees while working in their laboratories, fields, greenhouses, mechanical shops, and offices. Specific safety information is provided to all employees that perform tasks at this location, and all employees should know and understand the proper safety precautions they should take when performing their duties. This manual is a tool designed to be used by employees to facilitate the safety and well being of everyone at the USPSNL.
It's not possible to provide detailed information on the potential hazards associated with each and every task performed at the USPSNL. Anyone who performs tasks here bears the responsibility to examine their surroundings for unsafe acts or conditions and to immediately report them to their supervisor. When supervisors are presented with questions and concerns they are obligated to investigate and abate any unsafe environment. This manual will assist you in the recognition of potential problems and will guide you to successful and safe solutions. Safety's main component is common sense-using common sense will protect you and your coworkers from unnecessary injury.
Be your coworker's "keeper", because safety is YOUR responsibility.
Refer to the OCCUPATIONAL SAFETY & HEALTH PROTECTION FOR USDA EMPLOYEES Poster AD 1010 in the Lunchroom (G39) for complete information on Authorities, Agency Responsibilities, Employee Responsibilities, and Rights of Employees & Their Representatives.
NEED HELP? WHO YOU GONNA CALL?!
Your Supervisor: This is the first person to notify about an unsafe condition. He or she will immediately deal with the situation and will begin solving the problem.
USPSNL Safety Committee: These folks handle USPSNL safety problems on a regular basis. They research solutions and make recommendations to the Location Coordinator & Research Leader. Safety concerns that you have may be directed towards any member of the current (08/2002) committee:
- Kathie Moh, Environmental Protection Specialist / Safety Officer, 255-8849, Room G44
- Bill Shaben, Facilities Manager, 255-1065, Room G34
- Ray Glahn, Radiation Protection Officer / Research Physiologist 255-2452, Room 203
- Jennifer Williams, Biologist, 255-7744 / 255-0271, Room 322
- Mark Ramos, Entomologist, 255-0496, Room 331
USDA/ARS/North Atlantic Area Safety, Health, & Environmental Management Personnel: These folks oversee the safety and health programs of all NAA locations and are trained to provide safety, health, industrial hygiene, and environmental management services on an as-needed basis.
- Bonnie DiSalvo, Area Safety & Health Manager, (215) 233-6592
- Kathie Moh, Environmental Protection Specialist, Northern Cluster, 255-8849
- Glen Davis, Environmental Protection Specialist, Southern Cluster, (304) 725-3451 X309
EMERGENCY! EMERGENCY!
IN CASE OF AN EMERGENCY, CALL 911
In the event of an emergency all employees must evacuate the building according to the following plan:
- Employees on the GROUND FLOOR A-WING must evacuate through the WEST REAR DOORS.
- Employees in the GROUND FLOOR B-WING must evacuate through the CENTER REAR DOORS.
- Employees on the GROUND FLOOR C-WING must evacuate through the EAST REAR DOORS.
- Employees on the FIRST FLOOR A-WING, B-WING, and C-WING must evacuate through the FRONT DOORS.
- Employees on the SECOND FLOOR A-WING and B-WING must evacuate through the WEST REAR DOORS.
- employees on the SECOND FLOOR C-WING must evacuate through the EAST REAR DOORS.
- Employees on the THIRD FLOOR A-WING must evacuate through the WEST REAR DOORS.
- Employees on the THIRD FLOOR B-WING and C-WING must evacuate through the EAST REAR DOORS.
- Employees in the ATTIC must evacuate through the EAST REAR DOORS.
All employees should gather on the lawn BEHIND the building and account for one another.
Upon evacuation of your office or laboratory LIGHTS must be left ON and DOORS must be CLOSED.
- Bill Shaben is designated to ensure complete evacuation of the GROUND FLOOR
- Kathie Moh is designated to ensure the complete evacuation of the FIRST FLOOR
- Jon Hart is designated to ensure the complete evacuation of the SECOND FLOOR
- John Vandenburg is designated to ensure the complete evacuation of the THIRD FLOOR
- Employees on the GROUND FLOOR A-WING must evacuate through the WEST REAR DOORS.
- Employees on the GROUND FLOOR B-WING must evacuate through the CENTER REAR DOORS.
- Employees on the GROUND FLOOR C-WING must evacuate through the EAST REAR DOORS.
- Employees on the FIRST FLOOR A-WING, B-WING, and C-WING must evacuate through the FRONT DOORS.
- Employees on the SECOND FLOOR A-WING and B-WING must evacuate through the WEST REAR DOORS.
- Employees on the SECOND FLOOR C-WING must evacuate through the EAST REAR DOORS.
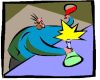
- Attend to any injured people: if they're on fire, get them to "stop, drop, and roll" and smother flames with a fire blanket.
- Alert others: yell "Fire!"
- Call 911 and activate the fire alarm.
- Close all doors and windows. Don't lock the doors.
- Evacuate the building. Don't use the elevator.
- Assist emergency personnel with the nature and location of the fire.
CHEMICAL SPILLS:
In case of a Major Chemical Spill:- Attend to injured people. Help them wash chemicals from their bodies by using emergency eyewash stations and emergency showers.
- Alert others.
- Avoid tracking spilled material to clean areas.
- Call 911.
- Close all doors and windows.
- Evacuate the building.
- Assist emergency personnel with the nature and location of the spill.
- Get help. Call Kathie Moh and/or Cornell EH&S.
- Use a Laboratory Spill Kit to clean spill.
- Repeatedly wash spill area.
- Contain clean-up material and dispose of properly.
PERSONAL INJURY/ILLNESS:
- Tend to the injured person.
- Chemical spill on body-wash immediately under emergency shower. Remove contaminated clothing.
- Chemical splash in eyes-rinse eyes for 15 minutes in an emergency eyewash.
- Alert others to the injury. If serious, call 911.
- Wash all cuts and puncture wounds and seek medical attention.
- Report all injuries to your supervisor and complete Form CA-1.
- Use a Laboratory Spill Kit to clean spill.
- Repeatedly wash spill area.
- Contain clean-up material and dispose of properly.
SEVERE WEATHER: Refer to the 01/14/00 Hazardous Weather Plan-Ithaca, NY Location Memo from Dr. B. B. Brodie (Appendix A). OR A-WING must evacuate through the WEST REAR DOORS.
EMERGENCY EQUIPMENT-KNOW WHERE IT IS AND HOW TO USE IT!

Attend the annual fire extinguisher training sessions coordinated by Kathie Moh. Don't use a fire extinguisher if you have no prior experience. Know where your fire extinguishers are. Make sure they are fully charged and make sure they are the right types for the material likely to catch fire. Remember that fire extinguishers are for small fires only-don't attempt to fight a large fire with one. In a large fire use the fire extinguisher only if the fire is between you and your exit. DON'T TRY TO BE A HERO. Let the professionals put the fire out. Think of your personal safety first.
USING EMERGENCY SHOWER STATIONS:
Know where your emergency shower station is. Do not block access to it at any time. Check the flow of water weekly to remove debris and bacteria. If chemicals soak your clothing, remove the clothing as you are soaking under the shower. DON'T BE SHY.
USING CHEMICAL SPILL KITS:
Know how to deal with a spill of a chemical BEFORE it spills. Read the chemical's MSDS. Familiarize yourself with the contents of a spill kit. Laboratories with acids and bases should have kits that will chemically neutralize and absorb acids and/or bases. Laboratories with flammable solvents should have kits with chemicals designed to readily absorb the solvents. Laboratories that use mercury and mercury thermometers should have kits designed to collect spilled mercury efficiently. Spill kits have the necessary personal protective equipment like gloves and goggles that are worn while cleaning the spill. Spill kits are mounted in hallways and in G26.
Spill kits are for "incidental" spills only: i.e. for spills that present minor safety and health hazards to employees in the immediate work area and to employees assigned to clean up the spill, for spills that do not have the potential to become an emergency within a short time period, and for spills that are limited in quantity, exposure potential, and toxicity.
If a spill is not "incidental", notify your supervisor and call 911. Students should never attempt to clean up a spill. See Appendix B for specific spill cleaning information.
ELECTRICAL POWER AND POTABLE WATER OUTAGES:
In the event of a power failure, evacuate the building. Chemical fumehoods will become inoperable during a power failure, allowing fumes from toxic chemicals being used in them to escape into the breathing zone of the laboratory occupants. Cap the chemical container, close the hood sash, and exit the building. Emergency lighting will illuminate the exit paths during a power outage.
In the event of a potable water outage, emergency eyewash and emergency shower stations will not function. Cease using hazardous chemicals immediately and exit the building.
LABORATORY SAFETY
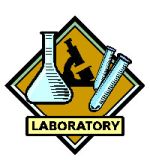
The Occupational Safety & Health Administration (OSHA) has enacted "Right to Know" legislation that requires employers to provide information to employees that alerts employees to the hazards they are exposed to or can be potentially exposed to while doing their jobs. You have the "right to know" what could hurt you while at work.
THE MATERIAL SAFETY DATA SHEET & CHEMICAL LABELS:
When working with chemicals it's vital that you understand the properties of those chemicals prior to using them. It's also your responsibility to understand what precautions to take when handling chemicals. The perfect tool for accomplishing this feat is the Material Safety Data Sheet (MSDS). There is an MSDS for every chemical in your workplace. A collection of MSDS's for all the chemicals at the USPSNL are maintained in binders in the Lunchroom (G39) and in individual laboratories. MSDS's are also electronically available at: http://www.arserrc.gov/naasafety/prod02.htm. The MSDS will tell you everything you need to know, from what the chemical's physical and health hazards are to what personal protective equipment (PPE) you must wear while using that chemical.
Another vital tool designed to communicate hazard information to the user is the Chemical Label. Labels contain the same vital information as MSDS's, but in a much more condensed fashion. Always read the label of a chemical prior to opening the chemical container, and never use a chemical that does not have a label.
CHEMICAL USE & YOUR HEALTH:

The USPSNL has an Occupational Health Maintenance Program (OHMP) which is designed to monitor your health and to measure the effect exposure to hazardous chemicals has on your health. All employees who use hazardous chemicals on the job are encouraged to participate in the OHMP, which is free of charge. Contact Sharon Maio, USPSNL Administrative Officer, for more information on the OHMP.
PROPER CHEMICAL STORAGE:
The best way to store chemicals is alphabetically, right? Wrong! Chemicals must be stored according to compatability. Keep acids away from bases, and oxidizers away from reducers and flammable solvents. Store flammable chemicals in flammable storage cabinets. In the laboratory, store only what you will use during the immediate future-limit quantities to 4 liters and under. Larger quantities of chemicals are stored in the Chemical Storage Room (G26). Never use fumehood workspace to store chemicals. When storing chemicals in glass containers always use secondary containment in case the glass breaks.
SAFE USE OF LABORATORY REFRIGERATORS & FREEZERS:
When liquids, gases, or solids having a flashpoint of less than 100 F must be stored in a refrigerator/freezer, the refrigerator/freezer must be rated to be "Explosion Proof" and "For Storage of Flammable Materials". Flammable vapors accumulate in the refrigerator/freezer and could ignite when a non-explosion proof refrigerator/freezer condenser or light turns on.
Because of cross-contamination possibilities, food should never be stored in a laboratory refrigerator that contains chemicals and other scientific samples. Laboratory refrigerators/freezers must be clearly marked with a "Store No Food" sign. Conversely, never store chemicals is refrigerators designed for food storage only (e. g. Lunchroom/G39 & Basement Stairwell).
CHEMICAL WASTE HANDLING & DISPOSAL PROCEDURES:
The laws set forth by the Resource Conservation and Recovery Act (RCRA) govern handling and disposal procedures of certain laboratory wastes that are categorized as hazardous. A waste is hazardous if it is listed in the Code of Federal Regulations or has the hazardous characteristics of being Ignitable, Reactive, Corrosive, or Extraction Procedure Toxic. Hazardous wastes generated in USPSNL must be managed properly. Containers of hazardous waste in the laboratories are clearly labeled as "Hazardous Waste", are made of chemically compatible shatterproof plastic, and are stored in secondary containment. Full containers of "Hazardous Waste" are taken from the laboratories to the Chemical Storage Room (G26). Hazardous wastes can never be poured down the drain or placed in the regular trash. The Environmental Protection Specialist conducts RCRA Hazardous Waste Management Training annually at the USPSNL. Hazardous Waste Guidelines are in Appendix C.
Disposal of certain non-hazardous chemical wastes is permitted according to the guidelines set forth by the Cornell University Guide for Drain Disposal of Laboratory Chemicals. These disposal policies are available electronically at http://www.ehs.cornell.edu/LRS/Waste_disposal.html#DISPOSAL OF LABORATORY WASTES
Always remember that "the solution to pollution is NOT dilution". If you are not sure of how to dispose of a chemical, ask your supervisor.
CHEMICAL ORDERING & REDISTRIBUTION:
Before ordering new chemicals you should consult the USPSNL central chemical inventory maintained by Mary Holmberg & Doris Corson to see if someone else has what you need. This helps to reduce the inventory of others while saving the USPSNL money. Avoid buying too large of a quantity of a chemical-it now costs many times more of the original purchase price to dispose of unwanted chemicals as hazardous waste. Buy just the amount you'll need for the job.
If you have an excess amount of a chemical, offer it to others at the USPSNL and Cornell for their use. Chances are the favor will be returned to you some day.
PERSONAL PROTECTIVE EQUIPMENT
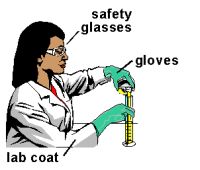
For new employees wondering what personal protective equipment (PPE) they need to wear, and for supervisors who are unsure as to what PPE their staff should be wearing, a Hazard Assessment Survey (Appendix D) has been developed to match the required PPE to the workplace hazard. A Hazard Assessment Survey should be conducted for each lab/workplace and posted in that area to alert all personnel to what the unique PPE requirements are. Your Area Safety & Health Manager, Environmental Protection Specialist, and/or Location Safety Officer is available to assist you in completion of the Hazard Assessment Survey. Personal protective equipment is always provided at no cost to the employee.
ENGINEERING CONTROLS:
The primary method of protection from hazards while in the laboratory are engineering controls like the chemical fumehood. Whenever possible, handle hazardous chemicals in the fumehood. Keep the glass sash between your face and the chemical-never stick your head inside the fumehood. Work a minimum of six inches into the fumehood to ensure maximum protection. Maintain proper airflow into and out of the fumehood by keeping supplies to a minimum. If you need to store equipment in the fumehood, "block" it up with a test tube rack (or something similar) to keep air moving freely under and around the equipment. Make sure your fumehood is working properly-if it is not, close the sash and notify your supervisor.
CLOTHING:
Protect your skin at all times. Wear pants and a lab coat whenever you work with chemicals. Always wear closed-toe shoes, no matter what the job. Steel-toe shoes are advisable when regularly handling heavy objects and when working on the farm. Wear safety glasses, splash goggles, and face shields when using chemicals, autoclaves, and mechanical shop equipment. Wear a hat and sunglasses and use sunscreen when working outside.
Wear the right gloves for the job-consult the glove information in Appendix E to make sure the gloves you wear provide for maximum protection and dexterity. Gloves need to be chemically and physically resistant to specific hazards you are exposed to. Ask your supervisor for help if you are unsure what gloves to wear.
RESPIRATORY PROTECTION:
A respirator must be worn when you are exposed to atmospheric contaminants potentially harmful to your respiratory system. Respirators are to be worn when you are exposed to pesticides, organic vapors and gases, resins, pigments, plasticizers, paints, laquers, enamel mists, metal fumes, silica, toxic dusts, smoke, asbestos, particulates, and dusts.
Before you can wear a respirator, you must receive medical clearance from an appointed physician stating that you are capable of wearing such a device. Participation in the Occupational Health Maintenance Program for respirator wearers is mandatory and free of charge. You must also receive a respirator fit test that measures how well a particular respirator fits your face and consequently how well you are protected from the respiratory hazard. A qualitative fit test is available from your Environmental Protection Specialist. A quantitative (and more definitive) fit test is available from Cornell University Environmental Health & Safety. Ask your supervisor to arrange for your fit test prior to performing any work which requires wearing a respirator. Consult your supervisor when deciding what the proper respirator for the job is. Obtain Respiratory Protection training from your Safety Officer and/or Environmental Protection Specialist to learn the proper techniques of respirator self-fit tests, sanitary storage, and cartridge maintenance.
HEARING CONSERVATION:
The USPSNL uses the Cornell University Environmental Health and Safety Hearing Conservation Program (HCP) to monitor noise levels and track employee exposures. The US Department of Labor's Occupational Safety and Health Administration's (OSHA) requirements for HCP's are used as a template for the program.
The services currently provides are: * Work Area Monitoring * Personal Employee Exposure Monitoring * Training on Noise Exposure Avoidance and Proper Hearing Protection Selection and Use
A good "rule of thumb" for determining if your work area of activity requires hearing protection is as follows: if you have difficulty hearing or understanding a "normal" tone of voice at a distance of three feet, noise levels are probably exceeding safe levels, and you should wear earplugs, hearing bands, or earmuffs. Contact your Safety Officer or Environmental Protection Specialist to determine what the right hearing protection equipment is for you.
DISPOSAL OF BROKEN GLASSWARE, SHARPS, NEEDLES, & SYRINGES:
Broken glassware should not be placed in the regular trash receptacles-each laboratory has rigid cardboard boxes designed and labeled specifically to safely contain sharp broken glass, used razor blades, scalpels, needles, and syringes. This sharps waste does not need to be treated as biohazardous waste unless it has been specifically used on animals and/or infectious material.
THE LAST WORD ON LAB SAFETY

Please use the following checklist as a tool to help make your laboratory as safe as it can be:
Chemical Storage
- Updated chemical inventory
- Chemicals dated upon receipt
- Chemical containers labeled, capped and in good condition
- No chemicals on, above or next to a desk
- No corrosive chemicals stored above "eye level"
- Chemicals segregated by hazard (organics from oxidizers, flammables from acids)
- Excess solvent stored in approved safety cans or solvent storage cabinets and not high up on shelving>/li>
- Approved safety cans equipped with self-closing lids and flame arresters intact
- Safety cans lids closed
- Safety cans/wash bottles properly labeled
- Waste containers labeled and chemical composition identified
- Biohazard containers used properly where needed (i.e. autoclave bags, sharps containers)
- Only "explosion proof" or "explosion safe" refrigerators/freezers may be used in labs to store flammables
- Refrigerators/freezers not "explosion proof" or "explosion safe" labeled NO FLAMMABLES ALLOWED
- Refrigerators/freezers labeled for "CHEMICAL USE ONLY" or "FOOD USE ONLY" and used accordingly
- Interior sound and free of chemical spills or contamination; containers stoppered or tightly closed
- Electrical apparatus equipped with ground plugs or properly grounded
- Extension cords in good condition (no splices)
- Extension cords for temporary use only, not overloaded and no longer than 6 feet
- Two prong appliances not within a 5-foot radius or directly located above flammables or sinks
- ppliances properly grounded
- All cylinders properly secured in an upright position, with cylinder clamp/chain fastened to solid support
- stored cylinders tightly capped and kept to a minimum
- Flammable materials stored a minimum of 20 feet from cylinders containing oxidizers
- Regulators, proper connections, and tubing in good condition
- Flammable gas tubing secured and labeled
- Flame arresters on flammable gas supply
- If toxic gases in use, proper leak sensors/alarms in place and regularly checked and calibrated
- If toxic gases or gases with poor warning qualities used (i.e. odorless); redundant systems; shutoffs in place in case of leaks/emergencies
- Exhaust hoods working, date of last inspection
- Hood sashes open and close and glass intact
- Hood free of excess chemical storage/equipment
- Hood sashes down (panels closed) when not accessing
- Fire Extinguishers
- Extinguishers in designated location and area labeled
- Extinguishers accessible and free from obstruction
- Current year and date of last inspection indicated on tag
- Labeled, accessible and free from obstruction
- Eye washes and drench hoses flushed weekly
- Safety showers flushed annually
- Kits in designated areas
- Inventory lists inside of First Aid kit
- First aid kit properly stocked
- Emergency PHONE# decals on telephone
- Safety glasses with side shields
- Substantial shoes, no sandals, open toes
- Protective clothing worn while working at bench
- Gloves selected according to hazard
- Chemical splash goggles where appropriate
- Vacuum pump belt guard in place
- Glass Dewars wrapped or shielded
- Protective shatter proof shield in place when in use
- Glass desiccators under vacuum stored in metal guards or shielded
RADIATION SAFETY
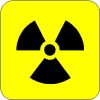
Laboratories and/or offices containing radioactive sources (sealed or unsealed) must have entry doors demarcated with a yellow "CAUTION RADIOACTIVE MATERIAL" sign. All USPSNL employees entering these areas must be made aware of the potential for exposure to radioactive material and must minimize exposure time, maximize exposure distance, and optimize exposure shielding to the fullest extent possible. No one under the age of 18 years may enter an area that contains radioactive material.
There are numerous licensed users of unsealed radioactive material at the USPSNL. The Location Radiation Protection Officer (LRPO) is Ray Glahn. Initial Radiation Safety Training is conducted by the LRPO. Radioactive stocks and wastes being held for decay are stored in Room G13. Radioactive wastes for disposal are stored in B? in the Greenhouse.
A complete guide to radiation safety may be found at the website of the USDA Radiation Safety Staff. All employees who work with radioactive material should go to http://www.usda.gov/da/shmd/rss1.htm and review the vital information presented there. Located at this website is the Radiation Safety Handbook which specifically outlines the responsibilities of all employees who use radioactive material.
Remember, you need to:
- Minimize your exposure TIME
- Maximize your exposure DISTANCE
- Use the appropriate SHIELDING
If you do that, your exposure to radioactivity will be ALARA:
As
Low
As
Reasonably
Achievable
FARM/RESEARCH PLOT SAFETY

SAFE USE OF FARM EQUIPMENT
- Working on a farm is a high-risk job. To prevent farming accidents, follow these guidelines:
- Get comprehensive training on how to safely operate machinery you will be required to use.
- Wear safety shoes at all times, especially when operating mowers.
- Wear leather gloves to protect your hands, earplugs to conserve your hearing, and safety glasses to save your eyesight.
- Wear the proper respirator when working in contaminated atmospheres.
- Don't smoke around gasoline or diesel fuel sources.
- When operating combustible engines indoors, use fans to rid your surroundings of exhaust.
- Don't use broken or damaged machines or tools-inform your supervisor of any problems with machinery.
- Immediately report all accidents and injuries to your supervisor.
PESTICIDE SAFETY
THE WORKER PROTECTION STANDARD TRAINING:
To protect you from exposure to pesticides while working with plants and/or pesticides, the U. S. Environmental Protection Agency issued a set of regulations known as the Worker Protection Standard (WPS). WPS training provides you with the information you need to know to protect yourself from exposure to harmful pesticides and is provided by Cornell University's College of Agriculture & Life Sciences. Any employee who works with plants and/or pesticides must receive this training. You will learn about the dangers of pesticides, the safety precautions you must take when working with plants and pesticides, the re-entry interval (REI) associated with pesticide applications, the content and location of the central information application notices, pesticide decontamination procedures, and personal protective equipment that is worn to prevent pesticide exposure.
EQUIPMENT HANDLING:
Pesticides should only be applied by trained and certified pesticide applicators. Refer to Appendix F for specific guidelines. Store all pesticide application equipment away from pesticides. Pesticide labels will tell you what personal protective equipment you need to wear. If a respirator is required, make sure that it is the right kind and that it fits you well. Wear eye and face protection when splashing is a possibility, especially when mixing and pouring pesticides. Wear the right gloves for the job-read the label and the MSDS to determine how to maximally protect yourself. Store all personal protective equipment away from any pesticide-contaminated area.
PESTICIDE APPLICATION PREPARATION:
Pesticide label directions and restrictions must be followed implicitly. Designate one area for storing, weighing, and mixing pesticides. Have plenty of soap and water nearby. Strive to prepare only the exact amount of pesticide you'll need and spray at times that minimize effects on co-workers. Properly post the areas to be sprayed and the central bulletin board with the name of the pesticide being applied and the re-entry interval. Notify all individuals in areas adjacent to where you will apply pesticides to allow for them to vacate if necessary.
PESTICIDE CLEAN UP & DISPOSAL:
Extra care must be taken to not pollute potable water systems. Do not use sanitary or storm drains to dispose of pesticide rinsate. Apply all pesticide rinsate to the area being sprayed.
Triple rinse all empty pesticide containers and application equipment. Thoroughly clean the pesticide preparation area and return pesticide stocks to the pesticide storage cabinet. Keep the pesticide storage cabinet locked at all times. Always store pesticides in their original containers.
Decontaminate personal protective equipment (PPE) prior to removal. Maintain a pesticide spill kit close to the area where pesticides are stored.
RECORDS:
New York State law requires that records of all pesticide applications be submitted to the NY Department of Environmental Conservation annually every January. Negative reporting is also required. The information required on this record includes the date and area of application, the name and amount of the pesticide applied, and the name of the pesticide applicator. This information must be posted on signs in areas where pesticides are applied as well on the central bulletin board. Each individual pesticide applicator must maintain his/hers own records.
GREENHOUSE/HEADHOUSE ETIQUETTE
The following guidelines have been developed for those working in the greenhouses:
- Keep hoses out of walkways.
- Keep nozzles off the ground.
- Clean up all material when you are finished working.
- Pesticides are to be applied by licensed applicators.
- Pesticides are to be stored in the pesticide storage cabinet.
- The pesticide cabinet is to be kept locked.
- The greenhouse is not to be used as a storage or construction area.
If you have any questions about any of the above points of greenhouse etiquette, please contact your Safety Officer.
DEFENSIVE DRIVING
A vehicle, whether it's a government vehicle or personal transportation, can be a deadly machine in the hands of a careless driver. Operation of a vehicle must be taken seriously--this powerful device must be used with respect. A good defensive driving attitude is the key to your safety on the road. Here are some tips that may help you be a better "defensive" driver:
- Always use your seat belt. This includes your lap belt as well as your shoulder belt. Both are necessary for safety. If your vehicle is equipped with an airbag, you must still use seat belts.
- Adjust all accessories. Insure that your mirrors are adjusted as well as your seat.
- Secure loose objects in the vehicle. If you must make an evasive maneuver in order to avoid an accident, an unsecured object (e.g., toolbox, brief case, etc.) may fly around in the vehicle and injure a passenger. Do not place a hard hat on the rear window shelf.
- Concentrate on your driving, rather than personal problems or your work. Be attentive to your own actions, the actions of others, and the roadway environment.
- Keep a safe stopping distance behind the vehicle in front of you. You should be able to prepare to stop within 2 seconds, whatever your speed. Remember, it takes the average person about 3/4 of a second to recognize a hazard after it is first seen and another 3/4 of a second to switch from the accelerator to the brake pedal. At 55mph, your vehicle covers a distance of more than 80 feet per second. You will have traveled about 120 feet before you actually began to brake
- Be very cautious when adjusting your car radio, using your mobile phone or handling any other device that will distract you from driving defensively.
- Never drink alcohol while operating a vehicle.
- Be alert to "blind spots" when changing lanes. Look all ways and always use turn signals.
- Keep a cool head. Don't drive aggressively and don't take chances. Don't become a victim of "Road Rage".
- Know and obey all traffic rules, regulations and laws.
Even if you personally obey all the driving rules, regulations and laws, you are still at risk for a vehicle mishap, serious accident or fatality, due to someone else's carelessness. If you follow the above tips, however, your chances of "survival"on the highways will be much higher.
OFFICE SAFETY
Offices present safety hazards which are less obvious than laboratories, but which are just as serious. It is easy to be injured if you are careless in an office, particularly around office machinery. Look for potential hazards and eliminate dangers before an accident occurs. In order to insure safe working conditions, observe the following:
- Keep aisles free of wastebaskets or other obstacles.
- Do not stretch electrical or telephone cords across walkways.
- Store heavy files in the bottom of filing cabinets. Only one drawer should be open at any one time.
- Use only approved fluids to clean electrical machines. Small sparks may ignite the cleaner.
- Use finger guards to avoid paper cuts when working with stacks of paper.
- Store pins, paper clips, thumbtacks, and other sharp objects in such a way that they will not stab anyone.
- Reducing glare with the help of proper lighting, maintaining screens to keep a sharp image, and resting your eyes periodically can minimize possible eyestrain from the use of video screens.
- Use a ladder or step stool for reaching high places. Never use a chair or something on wheels. Get help if you are lifting or moving heavy objects.
Everyone in each building, including clerical workers and visitors, should be aware of basic laboratory safety rules. Two of the most important ones to remember include:
- Read all safety signs posted in laboratories you enter.
- Know the locations of fire extinguishers, eye washes, and safety showers so that you can quickly assist with any emergency in nearby laboratories.
COMPUTER WORKSTATION ERGONOMICS
CHAIR ADJUSTMENT:
- Is your chair height adjustable?
- Does your chair support your lower back?
- Is there room between the front edge of the chair seat and the back of your knees?
- Can you easily reach your work without interference from the arms of your chair?
- When using the keyboard or mouse are you able to keep your arms in a comfortable position with elbows in at your sides?
- Do your feet rest flat on the floor or footrest?
- Are your knees bent at approximately 90-degree angles?
Sitting with your feet flat on the floor (or supported by a footrest) will help support your spine. Having your thighs parallel to the seat with knees bent at approximately a 90 degree angle and having adequate clearance behind your knees will keep the chair from interfering with the blood circulation in your legs. If the back of your chair is adjustable raise or lower it so that the contour of the chair provides maximum lumbar (lower back) support. If possible adjust the tilt of the backrest to support your body in an upright position. A slight angle either forward or back is also acceptable. Adjust the chair according to what is most comfortable for you. If your chair has arms they should allow you to get close to your work without getting in the way. If you are typing they should be at a height where they barely contact your elbows when your arms are resting comfortably at your side. Chair arms should not force you to elevate your shoulders or wing your arms to the side.
WORK SURFACE / KEYBOARD ADJUSTMENT
- With your chair adjusted properly is your keyboard at approximately elbow level?
- Are your arms in at your sides rather than stretched out in front of you?
- Are your shoulders relaxed and not elevated when you work at your work surface?
- When using the computer is there approximately a 90-degree angle between your forearms and upper arms?
- When using the computer are your wrists in line with your forearms and not bent upwards, downwards, or to one side or another?
- Is there at least 2 inches of clearance between the bottom of your work surface and the top of your thighs?
Ideally, with your arms resting comfortably at your sides, the home row of your keyboard (the row with letters a,s,d,f) should be at approximately elbow level. To easily check this, turn sideways to your keyboard. If your work surface is too high and cannot be adjusted, raise the chair to bring your elbows to the home row level of the keyboard and support your feet with a footrest if necessary. If your work surface is adjustable, start by adjusting your chair as described in the first section. Once the chair is adjusted, then adjust the work surface.
MONITOR ADJUSTMENT
- Is your monitor aligned in front of your keyboard rather than off to the side?
- Is the viewing distance to your computer monitor at least 18 inches?
- Is the top of the computer screen at or just below eye level?
- Is your computer monitor protected from excess glare?
- If you wear bifocals or trifocals, are you able to look at the monitor without tilting your head?
Position your monitor so it is aligned in front or nearly in front of your keyboard to allow your neck to remain straight when viewing the monitor. Raise or lower your computer monitor so that the top of the screen is at or just below eye level. You may need to unstack the monitor from the CPU to lower the monitor to the correct height or place a book or ream of paper between the monitor and CPU to raise it to the correct height. People who wear bifocals or trifocals often end up tilting their heads back to read through the lower portion of their glasses. Lowering the computer monitor by placing it directly on the desk surface typically helps. Bifocal users may want to discuss with their eye doctor the possibility of obtaining glasses specifically designed for computer use.
WORKSTATION ACCESSORY ADJUSTMENTS
- Are your input devices (mouse, trackball, digitizing tablet) at the same level and next to your keyboard?
- Are your primary work materials located in front of you?
- Are your most frequently accessed items (phone, manuals, etc.) easy to reach?
- Do you have a document or copyholder to hold reference material?
- Are you able to keep your arms from resting on any sharp or square edges of your work surface?
- If a large percentage of your time involves using a phone do you use a phone headset?
Computer input devices such as a mouse or trackball should be located at the same level and next to the keyboard to avoid reaching. This can sometimes be a problem if using a keyboard tray that is not wide enough to accommodate the keyboard and mouse. Modification or replacement of the keyboard tray may be necessary. As you change tasks, remember to move primary materials in front of you. If you must frequently look at reference materials as you type, you should consider a document holder to allow your head to remain in a more upright position. Position the document holder at the same height and distance as your monitor. If doing a lot of reading or writing on the desk, inclining the material by placing it on a 3-ring binder notebook helps reduce the need to bend the neck forward. The wrists should remain straight when typing. If you have poor wrist habits, a padded wrist rest can help support your wrists in a straight position. Height of the wrist rest should not exceed the height of the space bar on the keyboard. Avoid wrist rests that are wider than 3 inches since this results in the need to reach further for the keyboard. When talking on the phone it is not good for the neck to cradle the phone between your ear and shoulder. For jobs with a high volume of phone calls headsets are recommended since they allow you to maintain the head in an upright position when talking on the phone.
WORK HABITS When using a mouse, the mouse should be held lightly and movement of the mouse should occur from the shoulder instead of only at the wrist. When not actively using the mouse ease your grip on the mouse to let your hand relax. Periodic breaks help alleviate fatigue and strain to your eyes and upper body. Taking a break does not mean that you have to stop working. Rather it allows you to integrate other activities such as making phone calls, making copies, or talking with a co-worker. Changing positions periodically helps maintain circulation and prevents putting pressure on any one area of the body for an extended period of time. Working overtime or working under stress to meet deadlines can add to tension or discomfort. In addition to taking breaks and frequently changing positions you should pay attention to how your body responds to discomfort. Discomfort that goes away overnight can be a sign of fatigue. Discomfort that is continuous may build to a more serious problem. If you experience lasting discomfort please discuss this with your supervisor. Aches and pains that are addressed early typically resolve quickly. Ignoring pain prolongs and may even worsen the problem. Develop good habits outside of work. While you may not be able to adjust all of the work surfaces at home, you may be able to make minor adjustments that are significant to your body. Good posture and good work habits are just as important outside of work, whether you are using your home computer, doing chores around the house, or are involved in special projects or hobbies. HAZARD COMMUNICATION/RIGHT TO KNOW All USPSNL employees are required to receive initial and annual OSHA-mandated Hazard Communication / Right to Know training. This vital training helps you recognize the hazards you are exposed to or can be potentially exposed to while on the job. Steve Schaefer coordinates this training. HAZARDOUS WASTE MANAGEMENT UNDER RCRA All employees who generate or handle hazardous waste must receive initial and annual EPA-mandated Hazardous Waste Management under the Resource Conservation & Recovery Act training. This training allows for proper management and disposal of hazardous wastes. Steve Schaefer coordinates this training. LABORATORY SAFETY All employees who work in laboratories should receive training in all aspects of lab safety, including chemical safety, lab equipment safety, material safety data sheets, understanding chemical labeling, laboratory fumehoods, cleaning chemical spills, and personal protective equipment. Kathie Moh coordinates this training. FARM SAFETY All employees who perform work on a farm should receive training in safe usage of farm machinery and the Worker Protection Standard. Steve Schaefer coordinates this training. DEFENSIVE DRIVING All employees who drive government owned vehicles should receive defensive driving training. Kathie Moh coordinates this training. For further training information and to view the North Atlantic Area's Safety, Health, & Environmental Management Website, visit http://www.arserrc.gov/naasafety Here is the procedure to follow once new employees report for work. Keep in mind that this applies to every employee who performs tasks at this location: i.e. ARS or Cornell employees, full-time or part-time, scientists, technicians, administrative personnel, maintenance personnel, postdocs, graduate students, work-study students, summer workers, etc. New employees must receive ARS Safety Training regardless of what training they may have received elsewhere. There are no exceptions to this policy. Ideally, all new employees should receive safety training prior to performing any work. Supervisors are ultimately responsible for the safety of those who work for them. Follow these steps: A. MODERATELY OR HIGH-LEVEL HEALTH HAZARD SPILLS REQUIRING AN "EMERGENCY RESPONSE In the event of a moderately or high-level health and safety hazard chemical spill in which there is an immediate or potential injury risk to you or your coworkers, leave the area and contact your supervisor. Instruct all personnel in the spill area to leave the room with you. Secure the door and, if necessary, post signs to prevent entry. Dial 911 to alert the local emergency response team and be prepared to provide the following information: In the event of a fire resulting from a chemical spill, alert all co-workers working in the area by yelling "FIRE," PULL FIRE ALARM, alert your supervisor and contact the fire department (911). Do not attempt any spill response measures on burning chemicals or solvents. If this type of spill occurs inside the laboratory fumehood, completely close the fumehood sash. Wait for assistance in nearby safe area. Report all chemical and pesticide spills to the CEPS and the Location Administrative Officer. B. RESPONSE TO "INCIDENTAL" LOW-LEVEL HEALTH HAZARD SPILLS YOU MAY CLEAN UP A CHEMICAL SPILL SAFELY IF: SPILL CONTROL RESPONSE STEPS: IDENTIFICATION, HANDLING, STORAGE AND DISPOSAL OF CHEMICAL WASTES AND EXCESS CHEMICALS The purpose of this section is to provide guidance for the identification, handling, storage and/or disposal of chemical and pesticide wastes generated from the laboratory and field research activities conducted at the USPSNL. This facility is required to follow all EPA, State and Local regulations that govern landfill disposal of non-hazardous materials, EPA regulated disposal of hazardous wastes under RCRA (Resource Conservation and Recovery Act), non-domestic wastewater discharges, and air pollution standards. IDENTIFICATION OF HAZARDOUS CHEMICAL WASTES Every USPSNL employee should be aware of the dangers associated with the chemicals and pesticides that they work with or come into contact with based on chemical label warnings and information obtained from the MSDS. The potential for serious injury to employees, the general public or the environment is not diminished when a chemical or chemical mixture, generated from your research activities, becomes a waste. As such, the accurate identification of hazardous wastes and their proper handling to protect human health, animals and the environment is critical. EPA has published a list of hazardous chemical wastes (listed waste), typically associated with industry, in the Code of Federal Regulations 40 (Protection of the Environment) Part 261.33. Unfortunately, not all chemical wastes generated by USPSNL laboratories are listed and as such need to be evaluated by characteristics criteria established for "unlisted" hazardous waste. These characteristics are ignitability, corrosivity, reactivity, and toxicity. Toxic chemicals include carcinogens, teratogens, mutagens, poisons, and those containing heavy metals. All excess chemicals or chemical mixtures with components identified as listed or meet the criteria for characteristic waste will be disposed of through the USPSNL hazardous waste program. Guidance for the identification, handling and storage of hazardous materials or waste associated with any proposed or existing laboratory or field research activity is readily available from Kathie Moh. HANDLING AND STORAGE OF HAZARDOUS CHEMICAL WASTE When capturing hazardous chemical wastes of equal to or less than one gallon, clean glass bottles may be utilized. When capturing quantities greater than one gallon, utilize five-gallon HDPE drums. For collection of solid wastes such as gels, contaminated pipettes, gloves, broken thermometers, activated charcoal filters, and spill clean up materials, secure these materials in puncture resistant containers and sealed plastic bags. Unwanted or excess hazardous materials must be stored for disposal in individual containers. Do not deliberately mix hazardous wastes/materials together without contacting Kathie Moh. Hazardous material / hazardous waste must be properly labeled to identify the material and to warn personnel of the associated potential hazard(s). A hazardous waste label is to be secured on each container at the time of the initial waste generation and must include the following information: the words "HAZARDOUS WASTE," contents (individual percentages if a mixture), the start or beginning date of accumulation, and the waste generator's name. Preprinted hazardous waste identification labels are available in the Room G25. Any container used for storing hazardous waste must be kept closed during accumulation except when it is necessary to add or remove waste. A designated area within your laboratory will be marked with the sign "Satellite Accumulation Area" which is the temporary collection site for hazardous wastes. Within your satellite accumulation area, secondary spill containment is required for glass bottles containing hazardous wastes. Follow these procedures when disposing of hazardous waste: Guidance for the disposal of empty chemical bottles, metal cans, or pesticide containers is as follows: Empty bottles, cans or small drums that contained non-hazardous chemicals or materials can be disposed of by placing in the trash dumpster containing materials destined for the landfill. Empty bottles, cans or small drums that contained hazardous chemicals or materials must be completely emptied and rinsed thoroughly (triple-rinsed) prior to disposal directly into the trash dumpster. Personal Protective Equipment Requirements* Research Unit: ___________________________________ PI/SY:______________________________________ Signature:_____________________________________ Please complete Hazard Assessment as soon as possible, file the original, & post a copy in the lab., Hazard Assessments Check if Applicable Hazard in the Workplace PPE Requirement Glove selection is difficult for many lab staff. Different references seem to give conflicting information and the many available styles and types of glove materials add another layer of confusion. The process of glove selection can also be very time consuming. Consequently, many chemical users select a glove that may not be appropriate for the chemicals in use. Due to the recent publicity surrounding the death of a prominent Dartmouth researcher, Federal OSHA has placed a strong emphasis on hand protection in the workplace, especially in academic and R&D labs. The USPSNL will also be placing a similar emphasis on hand protection with written programs, training and participation in glove selection. Supervisors are responsible for the selection and application of gloves and other personal protective equipment in the workplace. The key to adequate glove selection is to only use the glove selection charts provided by the glove manufacturer for the glove in use and to not rely on other references. This is advisable since different manufacturers use different formulations for their polymers and a glove from one firm may not have the same chemical resistance as a glove which appears to be an identical glove made by another firm. Glove selection based on the manufacturers' glove selection charts is often impossible, as only a limited range of chemicals have been tested for use with a specific manufacturer's glove. In particular, many research grade chemicals are used in such small quantities that the various glove manufacturers will probably never test them. If a chemical is not listed on a glove selection chart it is advisable to have a specialist in personal protective equipment (PPE) make the glove selection for you. In this case the PPE specialist would attempt to match the known characteristics of the chemical to be used with the known characteristics of the polymers commonly used to make gloves to select a glove that would be appropriate. In some cases it may be required to hire a testing laboratory specializing in PPE to physically test a variety of gloves with the chemical to be used to scientifically select an appropriate glove. We have contacted a local testing firm that is capable of testing gloves for chemical resistance for a modest fee. If you have an especially hazardous chemical for which glove selection is difficult, we can make arrangements to have various gloves tested with the chemical in question. The glove selection for the materials listed below is offered for anyone using these chemicals at the USPSNL. If a particular manufacturer's glove charts vary from the glove selections below, follow the manufacturer's glove charts for the model of glove Latex gloves, especially thin, disposable exam gloves, are widely used in labs, shops and many other work environments. Our concern is two-fold: latex gloves offer little protection from commonly used chemicals and many people, up to 20% of the population by some estimates, are allergic to latex products. The use of latex gloves is only appropriate for: *Less than 1% for most hazardous chemicals or less than 0.1% if a known or suspect human carcinogen is in use in aqueous solution. Latex gloves offer no protection against many common lab and shop chemicals. They will severely degrade, often in a matter of seconds or minutes, when used with some materials. Staff required to wear latex gloves should receive training on the potential health effects related to latex. Hypoallergenic, non-powdered gloves should be used when possible. If a good substitute glove material is available, use gloves made of a material other than latex. General-purpose substitutes for latex products are lightweight nitrile gloves. Many of the recommendations below are for "incidental contact." This means that, as with many chemical procedures, no or very little actual contact with a chemical in use is anticipated. The gloves specified are basically there to prevent chemical contact with the skin when something goes wrong--a spill or splash to the hand, over spray from a dispensing device, etc. As soon as practical after the chemical makes contact with the gloved hand the gloves are removed and replaced. Often a glove specified for incidental contact is not suitable for extended contact, when the gloved hands may come into substantial contact with or actually may become covered with or immersed in the chemical in use. Generally speaking, a more substantial glove is required for extended contact than incidental contact, although there are exceptions. The practice of double gloving is recommended for many materials listed below. Two pairs of gloves are worn, one over the other. This affords a double layer of protection. If the outer glove starts to degrade or tears open the inner glove continues to offer protection until the gloves are removed and replaced. Best practice is to check the outer glove frequently, watching for signs of degradation (change of color, change of texture, etc.). With the first sign of degradation remove the outer glove and reglove. There are different approaches to double gloving. The most common practice is to wear a thin disposable glove (4-mil nitrile) under a heavier glove (8-mil nitrile). The outer glove is the primary protective barrier while the under glove retains dexterity and acts a vapor barrier in the event of mechanical failure or the permeation of the chemical in use through the outer glove. Alternately, you can wear the heavier (and usually more expensive and durable) nitrile glove as the under glove and wear thinner disposable nitrile gloves over those, changing the thinner outer gloves frequently. It is sometimes desirable to double glove with two sets of gloves made from different materials. Here, in the event of the failure of one material, the second, different material will act as a protective barrier until the gloves can be removed. The technique of using gloves of different materials is often advisable when a mixture of hazardous materials is in use. One type of material gives protection against one component or class of chemicals in the mixture and the second glove material gives protection against other components of the mixture. The requirements for double gloving and the materials of the gloves selected are specific to the chemical(s) in use. Glove Selection for Some Specific Chemicals in Use at the USPSNL Acetic acid (glacial or concentrated solutions): nitrile gloves (incidental contact); neoprene or butyl rubber gloves are recommended if contact with acetic acid above 10% is probable for an extended period of time. Acetic anhydride: double glove with heavier weight (8 mil) nitrile gloves (incidental contact) Acetic anhydride is very corrosive to human tissues (skin, eyes, and mucus membranes) and a poison by inhalation. For handling larger quantities of pure material only heavier weight (.28-. 33 mm) butyl rubber or neoprene gloves are recommended. Acetone: heavier weight (8 mil) natural rubber (incidental contact); for extended contact with acetone the only recommended glove type is butyl rubber. If you are cleaning parts with acetone, or have any other use of acetone where there is more than incidental contact, you must use butyl rubber gloves. Natural rubber gloves have about a 10-minute breakthrough time and are for incidental contact only. Nitrile gloves have a less than four-minute breakthrough time and are not recommended for any use of acetone. Acetonitrile: nitrile gloves or double glove with nitrile gloves (incidental contact) For transfer of acetonitrile or for large-scale use, only heavier weight butyl rubber or polyvinyl acetate gloves are recommended. Acetonitrile permeates though disposable latex exam gloves in a matter of seconds and latex gloves should never be used to handle this material. Acrylamide: nitrile gloves or double glove with nitrile gloves (incidental contact); butyl rubber gloves are recommended for extended contact (such as repackaging pure acrylamide into smaller containers) Acrylamide is readily absorbed through unbroken skin. Acrylamide is a carcinogen, mutagen, teratogen and a potent neurotoxin with no known antidote, so adequate hand protection is essential when using this chemical. Note that once acrylamide solutions are polymerized the resulting gels are no longer hazardous and, assuming that they are not contaminated with other hazardous materials, they may be disposed of in the ordinary trash. Bis- Acrylamide: nitrile gloves Bis-Acrlamide (N,N'-dihydrozy-ethylene-bis-acrylamide) does not share the more extreme toxic characteristics or acrylamide. However, it's toxicological properties have not been fully investigated and it should be treated as a hazardous material. Alkali metals (lithium, sodium, potassium, rubidium, cesium): nitrile gloves Note: It is very important that all work with alkali metals be conducted in the absense of water. Water forms hydrogen gas on contact with alkali metals. As this is a very exothermic reacion, working with alkali metals presents a severe fire hazard. All labs working with alkali metals much have a Class D fire extinguisher available. Ammonium hydroxide: nitrile gloves; for extended contact heavier weight neoprene or butyl rubber gloves are superior to nitrile gloves Benzotriazole, 1.2,3-: nitrile gloves Butanol ( and isomer): nitrile gloves (incidental contact); for extended contact, heavier weight butyl rubber or nitrile gloves are recommended Carbon disulfide: double glove with heavier weight (8 mil) nitrile gloves (incidental contact) or use 15 mil or heavier nitrile gloves; remove outer glove at once if exposed to carbon disulfide Carbon tetrachloride: double glove with heavier weight (8 mil) nitrile gloves (incidental contact) or use 15 mil or heavier nitrile gloves; remove outer glove at once if exposed to carbon tetrachloride Most nitrile gloves have a breakthrough time of only a few minutes and thus offer little protection when exposed to carbon tetrachloride. For operations involving the use of larger amounts of carbon tetrachloride, when transferring carbon tetrachloride from one container to another or for other potentially extended contact, the only gloves recommended are viton. Viton gloves are expensive, but they are the standard glove to use with carbon tetrachloride. Carbon tetrachloride is a poison, carcinogen, mutagen and teratogen. It is readily absorbed through unbroken skin. Alcohol and acetone are known to enhance the toxicity of carbon tetrachloride. The dose required to cause poisoning in humans varies significantly, with the ingestion of as little as 2 ml. having caused death. Carbon tetrachloride is also a substantial ozone depleting chemical and its use has been banned commercially. If you can find a substitute for carbon tetrachloride, it is strongly recommended that you use an alternative material. Catechol: nitrile gloves Chloroform: double glove with heavier weight (8 mil) nitrile gloves (incidental contact) or use 15 mil or heavier nitrile gloves; remove outer glove at once if exposed to chloroform Nitrile gloves have a 4-minute breakthrough time and thus offer little protection when exposed to chloroform. For operations involving the use of larger amounts of chloroform, such as transferring chloroform from one container to another or for large-scale extractions, etc., the only gloves recommended are viton or polyvinyl acetate (PVA). Viton gloves are expensive, but they are the standard gloves to use with chloroform. Chlorosulfuron: nitrile gloves Cobalt Chloride: See Heavy Metal Salts. Copper (Cupric) Sulfate: nitrile gloves Cryogenic liquids (liquid nitrogen, argon, helium, etc.): Cryogenic materials handling-rated gloves. Cryo-Gloves?, made by Tempshield, Inc., are highly recommended. Note that these gloves are made for handling very cold objects, but that they are not for immersion in liquid nitrogen or other extended contact with cryogenic liquids. 3,3'-Diaminobenzidine (DBA): nitrile gloves (incidental contact); double glove with nitrile gloves when handling the pure material or concentrated stock solutions Note: See Heavy Metal Salts for proper disposal of gloves and other dry waste contaminated with DBA. Diazomethane in ether (a derivatizing reagent): double glove with heavier weight (8 mil) nitrile gloves (incidental contact) or use 15 mil or heavier nitrile gloves; remove outer glove at once if exposed to diazomethane in ether. For possible extended contact, such as when transferring diazomethane in ether or when making reagent solutions containing this material, the only recommended glove would be a Norfoil glove, due to the extreme hazards associated with this material. Diazomethane is an extreme poison, a cancer suspect agent, extremely flammable, easily detonated and has an autoignition temperature of 100? C. (an ordinary light bulb would cause a sufficient quantity of the vapor in air to autodetonate). This is easily one of the most dangerous materials in use in labs at Cornell. If there is any way you can substitute another material for diazomethane in ether it is strongly recommended that you do so. Dichloromethane: See Methylene Chloride. 2,4-Dichlorophenoxy acetic acid (2,4-D): nitrile gloves Diethyl pyrocarbonate: nitrile gloves (incidental contact); double glove with nitrile gloves when handling the pure material or concentrated stock solutions Dimethyl sulfoxide (DMSO): heavier weight natural rubber gloves (15-18 mil; not 4 mil latex exam gloves) (incidental contact); butyl rubber gloves are recommended for extended contact; if you are allergic to natural latex products you may double glove with heavier weight (8 mil) disposable nitrile gloves (incidental contact) or use 15 mil or heavier nitrile gloves; remove outer glove at once if exposed to DMSO. Nitrile gloves are not recommended for use with DMSO if extended contact with the hands is expected. Some brands of nitrile gloves have degradation times of five minutes when used with DMSO. DMSO freely penetrates the skin and may carry dissolved chemicals with it into the body, so hand protection is especially important if you are working with any hazardous materials dissolved in DMSO. 1,4-Dioxane (dioxane): double glove with heavier weight (8 mil) nitrile gloves (incidental contact) or use 15 mil or heavier nitrile gloves; remove outer glove at once if exposed to dioxane Most nitrile gloves have a breakthrough time of only a few minutes and thus offer little protection when exposed to dioxane. For operations involving the use of larger amounts of dioxane, when transferring dioxane from one container to another or for other potentially extended contact, the only gloves recommended are butyl rubber gloves. Dioxane is one of the few commonly used lab chemicals that readily degrades viton gloves. Dioxane is only moderately toxic, but it is a listed carcinogen, mutagen and teratogen. It is readily absorbed through unbroken skin so hand protection is especially important when working with this material. Dithiothreitol: (Cleland's Reagent): nitrile gloves Ethanol: nitrile gloves Ethidium bromide: (EtBr): nitrile gloves (incidental contact); double glove with nitrile gloves when handling the pure material or concentrated stock solutions Note: See Heavy Metal Salts for proper disposal of gloves and other dry waste contaminated with EtBr. Ethyl acetate: double glove with heavier weight (8 mil) nitrile gloves (incidental contact) Nitrile gloves are not serviceable for extended contact as even heavy weight nitrile gloves (36 mil) have a breakthrough time of only 8 minutes and thus offer little protection when exposed to ethyl acetate. For operations involving the use of larger amounts of ethyl acetate, when transferring ethyl acetate from one container to another or for other potentially extended contact, the only gloves recommended are butyl rubber and polyvinyl acetate (PVA). Ethyl ether (diethyl ether, ether): double glove with heavier weight (8 mil) nitrile gloves (incidental contact) or use 15 mil or heavier nitrile gloves; remove outer glove at once if exposed to ether Ether is one of those chemicals that attacks almost all known commonly used glove materials. It permeates through viton, butyl rubber, neoprene, nitrile and natural rubber in a matter of minutes. The only recommended glove material for extended contact is polyvinyl acetate (PVA), such as the PVA? brand made by Ansell Edmont. Formaldehyde: nitrile gloves Formamide: nitrile gloves (incidental contact); butyl rubber gloves are the only gloves recommended for direct contact with the pure material. Formamide is often used in the pure form. If you use pure formamide in a procedure where there is probable contact with the skin, it is strongly recommended that you wear butyl rubber gloves. Formic acid: double glove with heavier weight (8 mil) nitrile gloves (incidental contact) Formic acid is very corrosive to human tissues (skin, eyes, and mucus membranes. For handling larger quantities of pure material only heavier weight (.28-. 33 mm) butyl rubber or neoprene gloves are recommended. Gallic acid: nitrile gloves Geneticin: nitrile gloves Glutaraldehyde: nitrile gloves Heavy Metal Salts (especially those that are easily soluble in water): nitrile gloves or double glove in some cases* For most inorganic (ionic) salts of heavy metals the human skin is usually an effective barrier against absorption of the heavy metal ions. If there are cracks in the skin, areas of inflammation, insect bites, cuts or other breaches of the integrity of the skin, heavy metal ions may be passed directly through the skin. The salts of many heavy metals are toxic or highly toxic and rated as poisons: arsenic, bismuth, cadmium, chromium, cobalt, lead, mercury, nickel, osmium and uranium. Some of these materials are also listed as corrosive (chromium trioxide), inhalation hazard (osmium tetroxide), known or suspect carcinogens and mutagens (lead and lead salts, mercury and its salts, etc.) or radioactive (uranium). Disposable nitrile gloves are generally acceptable for the use of the pure salts and stock (concentrated) or dilute solutions for the common salts of the above metals (acetates, chlorides, sulfates, nitrates, anhydrides, oxides, hydroxides, etc.) where only incidental contact will be made with these materials or their solutions. The skin more easily absorbs several heavy metal salts than others. Osmium tetroxide is readily absorbed by the skin and is very toxic. Lead acetate is absorbed 1-1/2 times more easily than other lead salts. Mercuric chloride can be absorbed fairly easily, especially if there are cracks, cuts or other breaks in the skin. It is also very toxic. It is recommended to *double glove* with nitrile gloves when using these materials, especially when handing the pure compounds or their strong solutions. Heptane: double glove with heavier weight (8 mil) nitrile gloves (incidental contact) or use 15 mil or heavier nitrile gloves For extended contact, as when using heptane for large scale extractions, refilling secondary containers or as a cleaning fluid, a heavier weight nitrile (35 mils or thicker), viton or PVA gloves are recommended. Note that the permeation time for heptane through 4 mil nitrile gloves is about 8 minutes and through latex exam gloves is even less time; subsequently, these gloves are not recommended for use with heptane. Hexamethylenediamine (1,6-diaminohexane): heavier weight (8 mil) nitrile gloves (incidental contact); use a heavier weight neoprene glove when handling the pure material or concentrated stock solutions (extended contact) Hexane: double glove with heavier weight (8 mil) nitrile gloves (incidental contact) or use 15 mil or heavier nitrile gloves For extended contact, as when using hexane for large scale extractions, refilling secondary containers or as a cleaning fluid, a heavier weight nitrile (35 mils or thicker), viton or PVA gloves are recommended. Note that the permeation time for hexane through 4 mil nitrile gloves is about 12 minutes and through latex exam gloves is only about 5-6 minutes; subsequently, these gloves are not recommended for use with hexane. Hydrochloric Acid (concentrated and strong solutions): nitrile gloves (incidental contact) A heavier weight neoprene or butyl rubber glove would be superior for long-term use with more concentrated solutions, such as cleaning glassware that has been soaking in an HCl bath or other larger-scale use of HCl. Hydrofluoric acid (HF): double glove with heavier weight (8 mil) nitrile gloves (incidental contact) or use 15 mil or heavier nitrile gloves Note that additional protective equipment must always be worn when using larger quantities of HF. Nitrile or rubber sleeves, rubber aprons, face shields and splash goggles (not safety glasses) should also be worn. All users of HF must maintain an HF first aid kit in their lab. Hydrofluoric acid (HF): double glove with heavier weight (8 mil) nitrile gloves (incidental contact) or use 15 mil or heavier nitrile gloves Note that additional protective equipment must always be worn when using larger quantities of HF. Nitrile or rubber sleeves, rubber aprons, face shields and splash goggles (not safety glasses) should also be worn. All users of HF must maintain an HF first aid kit in their lab. HF users are advised to contact EH&S for an "HF Users Information Packet." Hypophosphorous acid: double glove with nitrile gloves (4 mil) (incidental contact) or use 8 mil or heavier nitrile gloves Kananmycin: nitrile gloves Isoamyl alcohol: nitrile gloves Isoctane: nitrile gloves (incidental contact); for extended contact heavier weight nitrile gloves are recommended Isopropanol: nitrile gloves Lactic Acid: nitrile gloves (incidental contact); double glove with nitrile gloves or use neoprene or butyl rubber gloves if contact with lactic acid is probable for an extended period Laser dyes: nitrile gloves Lead Acetate: See Heavy Metal Salts. Laser dyes: nitrile gloves Mecuric Chloride: See Heavy Metal Salts. Methanol (methyl alcohol): nitrile gloves Methanol should never be allowed to make contact with the skin as it is fairly easily absorbed by the skin. Methanol is a poison. Methylene Chloride: double glove with heavier weight (8 mil) nitrile gloves (incidental contact) Methylene chloride will permeate through nitrile gloves in four minutes or less. If you are double gloved, as recommended, and you splash or spill methylene chloride on your gloves, stop what you are doing and change the outer glove immediately. If you allow methylene chloride to remain on the outer nitrile glove for more than two to four minutes you must discard both sets of gloves and re-double glove. Methylene chloride permeates though disposable latex exam gloves in a matter of seconds and latex gloves should never be used to handle this material. For use of methylene chloride where contact with the glove is anticipated, such as stripping paint or gluing plastics, only polyvinyl acetate (PVA) or viton gloves are recommended. These gloves come in .28-.33 mm thickness. PVA offers the best protection. Methyl sulfonic acid, ethyl ester (EMS) (ethyl methanesulfonate): nitrile gloves (incidental contact); double glove with nitrile gloves when handling the pure material or concentrated stock solutions Note: See Heavy Metal Salts for proper disposal of gloves and other dry waste contaminated with EMS. Monoethanolamine: nitrile gloves Nickel chloride: See Heavy Metal Salts. Nitric acid: double glove with heavier weight (8 mil) nitrile gloves (incidental contact); remove outer glove at once if exposed to nitric acid Light weight nitrile gloves are not recommended for any use with nitric acid as they are degraded very quickly. Even heavier weight nitrile gloves last only five minutes or less in contact with nitric acid. For handling larger quantities of concentrated nitric acid, or for extended contact, only heavier weight (.28-.33 mm) butyl rubber or neoprene gloves are recommended. N-Methylethanolamine: double glove with heavier weight (8 mil) nitrile gloves (incidental contact); remove outer glove at once if exposed to N-methylethanolamine Viton, neoprene or butyl rubber gloves are recommended for extensive use of N-methyl-ethanolamine such as working with the pure material or making solutions. Octane: nitrile gloves (incidental contact); for extended contact heavier weight nitrile gloves or viton gloves are recommended Organophosphorous compounds: double glove with heavier weight (8 mil) nitrile gloves (incidental contact) or use 15 mil or heavier nitrile gloves Osmium Tetroxide: See Heavy Metal Salts. Paraformaldehyde: nitrile gloves Pentane: double glove with heavier weight (8 mil) nitrile gloves (incidental contact) Thin nitrile gloves are quickly degraded by pentane. For extended contact with pentane only heavier weight neoprene gloves or viton gloves are recommended. Pesticides: heavier weight unlined nitrile gloves (8-20 mils) or a glove specified by the pesticide label.* A wide variety of pesticides are in use at Cornell. Each EPA registered pesticide is provided with an MSDS-like label. The pesticide label may have a glove selection category listed on the it which is based on the "EPA Chemical Resistance Category Selection Chart." The glove selection category is listed as A through H, with each category representing a group or class of pesticides. If the label specifies a glove type, the applicator must wear the specified glove. Additional information on the selection of gloves for the use of various pesticides may be obtained from Mary-Lynn Cummings at 255-2557 or the Pesticide Management Education Program at 255-1866 Perchloroethylene (tetrachloroethylene): Double glove with heavier weight (8 mil) nitrile gloves (incidental contact); remove outer glove at once if exposed to perchloroethylene. For extended contact, such as parts washing, heavier weight nitrile gloves (22 mil or heavier, such as Ansell Edmont Sol-Vex brand, #37-165) may last up to five hours. Viton gloves are recommended for repeated extended contact with perchloroethylene. Thin (4 mil) nitile gloves have a breakthrough time of 4 minutes or less; neoprene and vinyl glove have a breakthrough time of less than 10 minutes; none of these materials are suitable for use with perchloroethylene. Petroleum ether: nitrile gloves (incidental contact); or heavy weight nitrile or viton for extended contact. Phenol: double glove with heavier weight (8 mil) nitrile gloves (incidental contact); neoprene or butyl rubber gloves are recommended for extensive use of phenol such as working with the pure material or making solutions. Nitrile gloves have a 30-minute breakthrough time with phenol. If working with double gloved nitrile gloves, change the outer glove frequently if exposed to this material. Phenol-chloroform mixtures: double glove with heavier weight (8 mil) nitrile gloves (incidental contact) or use 15 mil or heavier nitrile gloves; remove outer glove at once if exposed to mixture Viton gloves are recommended for work with phenol-chloroform mixtures when probable exposure to the mixtures exists, such as when making up the mixtures. See the entries for phenol and chloroform. Phenylmethylsulfonyl fluoride (PMSF): nitrile gloves (incidental contact); double glove with nitrile gloves when handling the pure material or concentrated stock solutions Phenylmethylsulfonyl fluoride is corrosive (causes burns) on contact with the skin, eyes and mucus membranes. It is also a highly toxic cholinesterase inhibitor and central nervous system poison. Avoid all contact. Note: See Heavy Metal Salts for proper disposal of gloves and other dry waste contaminated with PMSF. Phosphonic acid: double glove with nitrile gloves (4 mil) (incidental contact) or use 8 mil or heavier nitrile gloves Phosphoric acid: double glove with nitrile gloves (4 mil) (incidental contact) or use 8 mil or heavier nitrile gloves Picloram (4-amino-3,5,6-trichloropicolinic aicd): nitrile glove Polychlorinated biphenyls (PCBs): For weighing out of pure or concentrated materials, wear an 8 mil or heavier nitrile glove over a neoprene glove. For dilute solutions in corn oil (1 p.p.m. or less) neoprene gloves (20 mil) are recommended. Polyoxyethylenesorbitan monolaurate (Tween 20): nitrile gloves Potassium ferricyanide: nitrile gloves Potassium ferrocyanide: nitrile gloves Potassium permanganate: nitrile gloves Propanol: nitrile gloves Propionic acid: nitrile gloves (incidental contact); neoprene or butyl rubber gloves are recommended if contact with propionic acid is probable for an extended period of time. Propylene oxide: heavier weight (17 mil or greater) butyl rubber or neoprene gloves (incidental contact); norfoil gloves are the only glove recommended for extended contact Propylene oxide attacks almost all common glove materials. It passes directly through latex gloves and the breakthrough time for nitrile gloves ranges from seconds to a few minutes. Ordinary 4 mil latex and nitrile lab gloves should never be used with this material. Propylene oxide has a breakthrough time of only 10 minutes with viton gloves which are completely resistant to most common lab chemicals. The breakthrough time for neoprene and butyl rubber gloves is on the order of 45-50 minutes. Use heavier weight gloves (17 mil or greater), check the gloves often and discard after 40 minutes or so or of continuous use when there is contact of propylene oxide with the glove. When possible, use a norfoil glove with a heavier weight (8 mil) nitrile Psoralen: nitrile gloves (incidental contact); double glove with nitrile gloves when handling the pure material or concentrated stock solutions Psoralen is corrosive (causes burns) on contact with the skin, eyes and mucus membranes. It is anticipated to be carcinogen, it is a mutagen and a strong photosensitizer. Avoid all contact. Note: See Heavy Metal Salts for proper disposal of gloves and other dry waste contaminated with psoralen. Pump oil: butyl rubber gloves If you are changing pump oil or servicing pumps where contact with the oil may occur, the only recommended glove type is butyl rubber. Silane based silanization or derivatization compounds: double glove with heavier weight (8 mil) nitrile gloves (incidental contact) or use 15 mil or heavier nitrile gloves; remove outer glove at once if signs of degradation occur Silver nitrate: See Heavy Metal Salts. Sodium dodecyl sulfate (SDS): nitrile gloves Sodium azide: nitrile gloves or double glove with nitrile gloves (incidental contact) Spermidine: nitrile gloves Sulfuric acid: heavier weight (8 mil) nitrile gloves (incidental contact); heavier weight (20 mil or greater) neoprene or butyl rubbber gloves (extended contact) Tetrahydrofuran (THF): double glove with heavier weight (8 mil) nitrile gloves (incidental contact) or use 15 mil or heavier nitrile gloves; remove outer glove at once if THF contacts glove For extended contact, such as when using THF for larger scale reactions, refilling secondary containers or as a cleaning fluid, only Norfoil gloves are recommended. Polyvinyl acetate (PVA) gives some limited protection (up to 1-1/2 hours for some gloves) but are inferior to the Norfoil gloves. Note that the permeation time for THF through 4 mil nitrile gloves and latex exam gloves is almost instantaneous; subsequently, these gloves are not recommended for use with THF. Testosterone: nitrile gloves (incidental contact) 3,3',5,5'-Tetramethylbenzidine (TMB): nitrile gloves (incidental contact); double glove with nitrile gloves when handling the pure material or concentrated stock solutions Note: See Heavy Metal Salts for proper disposal of gloves and other dry waste contaminated with TMB. N, N, N', N'-Tetramethylethylenediamine (TEMED): nitrile gloves (incidental contact); double glove with nitrile gloves when handling the pure material or concentrated stock solutions TEMED is corrosive (causes burns) on contact with the skin, eyes and mucus membranes. Timetin: nitrile gloves Toluene: double glove with heavier weight (8 mil) nitrile gloves (incidental contact) or use 15 mil or heavier nitrile gloves; remove outer glove at once if exposed to toluene For extended contact, such as when using toluene for larger scale reactions, refilling secondary containers or as a cleaning fluid, only viton or polyvinyl acetate (PVA) gloves are recommended. Note that the permeation time for toluene through 4 mil nitrile gloves is less than 4 minutes and through latex exam gloves is less than that; subsequently, these gloves are not recommended for use with toluene. Trichloroethylene: double glove with heavier weight (8 mil) nitrile gloves (incidental contact); remove outer glove at once if exposed to trichloroethylene For extended contact, such as when using trichloroethylene for larger scale reactions, refilling secondary containers or as a cleaning fluid, only viton or polyvinyl acetate (PVA) gloves are recommended. Note that the permeation time for trichloroethylene through even heavy weight nitrile gloves (36 mil) is 4 minutes, and only 10 minutes for even heavier butyl rubber gloves (64 mil). The permeation time for thin nitrile or latex exam gloves (3-4 mil) is on the order of a minute or two; subsequently, these gloves are not recommended for use with toluene. Trichloromethyl chloroformate (diphosgene): This chemical, usually supplied in sealed glass ampules, is very air/moisture reactive, a corrosive and it is considered to be highly toxic by all routes of exposure. It must be used in a vented glove box or environmental chamber under dry nitrogen or argon. Glove boxes are usually fitted with substantial butyl rubber gloves, however, one manufacturer recommends that "heavy" gloves be worn over the glove box gloves. I would recommend using 8 mil or heavier nirtile gloves over the butyl rubber glove box gloves. Please contact EH&S if you have any questions concerning the special procedures required for the use of this chemical. Triton-X100: nitrile gloves Valeric acid: nitrile gloves (incidental contact); double glove with nitrile gloves or use neoprene or butyl rubber gloves if contact with valeric acid is probable for an extended period Xylene: nitrile gloves (incidental contact) For use of xylene where contact with the glove is anticipated, such as pouring of new or used xylene into containers or other operations, polyvinyl acetate (PVA) or viton gloves are recommended. Welcome to the U. S. Plant, Soil, & Nutrition Laboratory! In an effort to determine what safety training you are required to receive, please answer the following questions. Consult with your supervisor and/or the safety officer if you are unsure how to answer. Please sign, date, and return to the Safety Officer. Remember that safety training should be completed prior to working. NAME_____________________________________________ SUPERVISOR______________________________________ DATE_____________________________________________ Employee ____________________________________ Supervisor ____________________________________ Date _______________________ The results of the New Employee Safety Training Requirement Survey indicate that you are required to receive the safety training listed below. When your requirements are met please complete to New Employee Safety Checklist with your supervisor and return it to the CEPS. You are required to watch the following videos that are highlighted: USDA Employee Rights & Responsibilities You are required to read the following manuals that are highlighted: USPSNL Chemical Hygiene Plan You are required to attend the following training seminars that are highlighted: Consult with CEPS to view videos and to schedule required training. THE SUPERVISOR HAS DISCUSSED THE FOLLOWING WITH ME: I. Chemical Safety ____1. No mouth pipetting. ____2. No food, drink, or smoking in lab. ____3. Laboratory coat must be worn when working in lab. ____4. No open-toed shoes or sandals allowed in the lab. ____5. Ice machines and microwave ovens designated for research use must NOT be used for food items. ____6. Soluble organics (250 ml or less) NOT on the EPA hazard list may be flushed down the sink in accordance with SOP for drain disposal. Water should be left running for at least 1 minute. Amounts greater than 250 ml must be discarded according to the procedures of the location. Do NOT dispose of any soluble organic that could be a suspected carcinogen, mutagen or teratogen, e.g. methylene chloride; consult with supervisor to make special arrangements in consultation with qualified safety personnel. ____7. Insoluble organics in relatively small quantities should be discarded in approved safety cans. The compound name, estimated amount and date should be recorded on tape and placed on the container to be collected by the CEPS and disposed of by vendor. ____8. Flammable compounds must be stored in approved flammable storage cabinets or in explosion-proof refrigerators/freezers. Working quantities only will be stored in the lab. Larger quantities (bulk) are stored in the solvent room. ____9. Acids (large bottles of concentrated acids) must be stored in a vented cabinet or under a hood. Do NOT store them in the same cabinet with organic solvents. ___10. Bases (large bottles of concentrated bases) must be stored in plastic carrying bottles. Do NOT put them in the acid storage cabinet or store them with organics. ___11. All noxious or hazardous compounds must be used in an operable hood. For extremely toxic compounds (i.e. cyanates), please notify on-site contractors before using in the hood so that personnel working on the roof can be protected from exposure. ___12. Wear gloves when appropriate. If necessary, wear 2 pair, changing the outer pair as required. ___13. Wear safety glasses or regular glasses at all times when you are working with hazardous materials or procedures in the lab. For especially dangerous operations, wear goggles or face shields for extra protection. ___14. Wear respirators or breathing masks as required. See lab supervisor concerning the appropriate choice of respiratory protection depending on the task or chemical to be used. ___15. Ask for assistance when lifting heavy (>20 lbs.) or bulky objects. ___16. Use safety step stool for retrieving objects higher than you can comfortably reach. ___17. Protect your eyes and exposed skin from UV (ultraviolet light) irradiation with appropriate eyewear or by leaving room during use of UV lamps. ___18. Disposal of especially toxic or hazardous substances (e.g. ethidium bromide) has been discussed with supervisor. II. Radiation Safety ____1. All personnel should be aware of NRC Notice to Employees posted near the entrance to rooms where radioisotopes are stored or used. ____2. All personnel working in the lab will be provided with radiation badges and finger rings (if they are using 32P) for monitoring exposure to radioisotopes used in the lab. ____3. All personnel working the laboratory have discussed with the supervisor aspects of radiological safety, including exposure to radiation, labeling of radioactive substances, the locations of radioactive wastes and stock solutions and what to do in the event of accidental spills and/or exposure. ____4. Personnel working with 32P have read RSS safety flyer entitled: Safety Requirements for Use of Phosphorus-32. ____5. Personnel working with 3H have read RSS safety flyer entitled: Safety Requirements for use of Tritium. ____6. Personnel working with any radioisotope have read the Radiation Safety Manual from RRS for use with radioisotopes and are aware of the location of a copy of 10CFR20. ____7. The supervisor and employee who will use radioisotopes have discussed how to clean up minor spills and contamination. ____8. The supervisor and employee have discussed what to do in the event of a major spill or gross contamination. ____9. The supervisor and employee have discussed how to dispose of the radioisotopes that will be used by the employee while performing experiments. Employee is also aware of standard disposal procedures for decay of 32P (aqueous and solid waste), dilution of 35S (aqueous) and by contractor (solid/scintillation fluid waste, 35S, and scintillation fluid waste, 32P). ___10. The supervisor and employee have discussed personnel protection and the use of shielding provided by the lab. ___11. The employee knows 1) to survey with the Geiger counter provided, the lab areas where isotopes have been used after each experiment and to record these results once a month for both radiation levels and removable contamination on the diagram provided by the laboratory; 2) to survey himself with the Geiger counter after each experiment and record the results before leaving the lab for lunch and at the end of the working day in the log book provided (employee knows to remove his lab coat and wash his hands each time before leaving the laboratory when isotopes have been used, except when transporting radioactive material from the lab); 3) to survey himself and any containers of radioisotopes to be transported from the lab to insure that all are at background levels before transporting radioactive substances from one room to another; 4) to survey his lab coat and de-contaminate it if necessary before it is sent for laundering. ___12. Employee must check each new experimental procedure to determine where radioisotope is going during the experiment. Also, any major modifications of a routine procedure should be checked. The information must be recorded in the permanent lab book of the employee and be available to the approved user when required. All experimental procedures using radioisotopes will be discussed with the approved user in advance and monitored by the approved user the first time it is performed. ___13. Employee has been instructed in the appropriate use of the survey and measuring instrumentation provided. ___14. Employees working with radioisotopes have filled out appropriate section of AD803 (Training Form) and have exposure records from previous positions where radioisotopes were used. III. Recombinant DNA Safety ____1. All lab personnel will wash their hands before leaving the lab area. Lab coats will be left in the lab when not in use. Wearing coats outside the lab should be restricted to areas where contact of non-research personnel is at a minimum and only when necessary for the employee's own protection. Lab coats should be placed in a plastic bag and taken for cleaning when appropriate. Contaminated coats will be autoclaved before laundering. ____2. The supervisor and employee have discussed clean up and de-contamination of bacteria and bacteriophage spills in the lab. ____3. The supervisor and employee have discussed the safe disposal of all contaminated materials (liquids and solids). ____4. Employee has read a recent coy of the NIH guidelines for working with recombinant DNA. ____5. Employee has read a copy of the University of Georgia Biosafety Manual or other appropriate guidelines respecting recombinant DNA research. IV. Grinding Room Safety ____1. Hearing and eye protection must be worn at all times. ____2. Compressed air can cause bodily injury if directed onto the skin surface and should not be used as a method of cleaning dust from clothing. Grinders must be turned off before attempting to clean the mill with compressed air. ____3. Hood filter system must be operating when using grinders. ____4. Personnel should maintain a clean working area at all times. V. Field Safety ____1. Upon arrival at any farm site, personnel must stop and check the Worker Protection Information Center where areas of pesticide application and reentry periods are identified. ____2. Personnel without a Pesticide Applicator License must receive and document Worker Protection training. ____3. Personnel must receive and document training in equipment operation. Warnings posted on equipment must be read and understood. ____4. Personnel performing fieldwork should attend the annual Cornell University "Safety Training Session" held each spring. ____5. Loose fitting clothing should not be worn to prevent getting caught in moving parts of machinery. ____6. Hearing protection must be worn when operating machinery. ____7. Equipment must not have riders other than the operator. ____8. No open-toed shoes or sandals allowed in the field. ____9. Employee has been cautioned about the effects of sun exposure and the location of protection products. VI. Vehicle Safety ____1. Vehicle operators will comply with all State and local laws and regulations. Vehicles should be operated at posted speed limits at all times. ____2. Vehicle operator is responsible for seeing that all seat belts are used when the vehicle is in motion. ____3. Vehicle operators will not furnish transportation to anyone other than those conducting official Government business. ____4. In the event of an accident, the operator of the vehicle must stop immediately & determine the extent of personal injuries and property damage; assist the injured in obtaining medical help; report the accident to the operator's official supervisor and to the State, county, or municipal authorities; give driver's name, address and organizational unit and obtain the same from the other party(s); obtain vehicle and driver's license number of all parties involved; and, obtain the names and addresses of witnesses, if any. ____5. Employee is aware that it is the vehicle operator's responsibility to pay any fines imposed for traffic law violations, including parking violations. VII. Emergency Procedures ____1. Employee has been provided with a copy of the fire and hazardous weather plans used by the location. ____2. Employee is aware that all accidents and injuries must be reported to the supervisor, Research Leader, or Administrative Officer. ____3. Employee has been shown the location of fire extinguishers in the laboratory, offices and in the hallways close by and been instructed in their use. Demonstrations of the extinguishers in the hallways can be provided by appropriate personnel upon request. ____4. In the event of any potentially serious accident (e.g. buildup of toxic fumes, etc.), employees WILL EVACUATE THE AREA IMMEDIATELY. After employees are safe, they will immediately notify the supervisor, Research Leader, Administrative Officer, or any appropriate personnel (e.g. ambulance, if deemed necessary). Employee's Signature and Date____________________________________ Supervisor's Signature and Date___________________________________ SAFETY TRAINING REQUIREMENT
NORTH ATLANTIC AREA
SAFETY, HEALTH, & ENVIRONMENTAL
MANAGEMENT WEBSITENEW EMPLOYEE SAFETY ORIENTATION
STUDENT EMPLOYEE POLICY
APPENDIX B
APPENDIX C
APPENDIX D
REQUIRED LABORATORY HAZARD ASSESSMENT SURVEY
OSHA Standards 29 CFR 1910.132-138
Lab Rooms: ________________________________________
Person completing survey: __________________________
Date: ______________________________________
*Refer to Appendix E for specific information on glove selection.Hazardous Liquids Chemicals Corrosive Liquids (Acid/Caustic)
Small Containers < l liter
Large containters >1 Liter Safety goggles, gloves*, long sleeved lab coat, and closed toe shoes
Safety goggles, gloves, long sleeved lab coat, rubber apron, closed toe shoes. If potential for a splash is high, it is advisable to use both face shield and goggles. Also if work is done on an open bench and not in a chemical fume hood, it is recommended that a face shield be used in addition to gogglesFlammable Liquids
Dispensing from 5 gallon drumsSafety goggles, gloves*, long sleeved lab coat, closed toe shoes
Safety goggles, gloves, long sleeved lab coat, closed toe shoes. If potential for a splash is high it is advisable to use a face shield in addition to gogglesHighly reactive liquid chemicals and high energy oxidizers Safety goggles, long sleeved lab coat, gloves*, closed toe shoes. Face shield or body shield must be used in addition to protective eyewear during the reaction based on the scale of the reaction Liquids with high acute toxicity (poisons) Safety goggles, gloves*, long sleeved lab coat, impermeable apron, closed toe shoes. If potential for a splash high use impermeable coveralls and a face shield in addition to goggles Liquids with high chronic toxicity (known and suspected carcinogens, reproductive toxins) Safety goggles, gloves*, long sleeved lab coat, closed toe shoes. Other hazardous liquid chemicals (not included in the above categories Safety goggles, gloves*, long sleeved lab coat, closed toe shoes. SOLID CHEMICALS Caustic solids (lime, etc.) Safety glasses, gloves*, long sleeved lab coat, closed toe shoes. If potential for getting a chemical into the face is high use face shield in addition to glasses. Flammable solids (alkali metals, red phosphorus, etc.) Safety glasses, gloves*, long sleeved lab coat, closed toe shoes. Highly reactive solids & high energy oxidizers Safety glasses, gloves*, long sleeved lab coat, closed toe shoes. Face shield or body shield during reaction based on the scale of the reaction based on the scale of the reaction in addition to protective eyewear. Solids of high acute toxicity (poisons) Safety glasses, gloves*, long sleeved lab coat, closed toe shoes. If weighing, use particulate mask or vented balance enclosure. If potential for disseminating powder high, use protective coveralls and a face shield in addition to glasses and a mask. Solids of high chronic toxicity (carcinogens and reproductive toxins) Safety goggles, gloves*, long sleeved lab coat, closed toe shoes. If weighing, use particulate mask or vented balance enclosure. Other hazardous solid chemicals (not included above) Safety goggles, gloves*, long sleeved lab coat, closed toe shoes. Compressed toxic gases Safety goggles, gloves*, long sleeved lab coat, closed toe shoes. Work with pressurized glass/plastic vessels (potential for creating flying fragments) Face shield, safety goggles, long sleeved lab coat, gloves*, closed toe shoes. LIGHT RADIATION Welding: Electric arc Welding helmet or shield worn over spectacles or goggles, gloves*, long sleeved lab coat, closed toe shoes. Protection from light radiation is directly related to filter lens density. Select the darkest shade that allows task performance. Welding: Gas Welding goggles or face shield worn over spectacles or goggles, gloves*, long sleeved lab coat, closed toe shoes. Cutting, torch, brazing, torch soldering Spectacles or welding face shield worn over spectacles or goggles, gloves*, long sleeved lab coat, closed toe shoes. Lasers
Class IIIb or IV Protective Laminated Glass Technology eyewear for the Narrow or Broadband Spectrums. Sources of UV light (hand hold irradiators, UV screens, germicidal lamps)
Class IIIb or IV UVA/UVB-blocking safety glasses, long sleeved lab coat, gloves*. Based on the duration of exposure and the source it may be advisable to use a UVA/UVB-blocking face shield worn over glasses. DUST Nuisance Dusts (woodworking, buffing, plant/soil grinding, general dusty conditions) Goggles, N95 Particulate Respirator (dust mask). TEMPERATURE EXTREMES Heat (hot surfaces, hot solutions, etc.)
Cold Low temperature freezers
Cryogenic gases
(N2, He2, etc.)Face shield, thermal gloves, long sleeved lab coat, closed toe shoes.
Thermal gloves, long sleeved lab coats, closed toe shoes.
Face shield, thermal gloves, long sleeved lab coat, closed toe shoes. Autoclave operation Face shield, rubber apron, thermal gloves, lab coat, closed toe shoes.. APPENDIX E
Hand Protection and Glove Selection Including Glove Selection for Some Specific Chemicals
APPENDIX F
STANDARD OPERATING PROCEDURE FOR PESTICIDE APPLICATIONS
APPENDIX G
NEW EMPLOYEE SAFETY TRAINING REQUIREMENT SURVEY
APPENDIX H
EMPLOYEE SAFETY TRAINING REQUIREMENTS
U. S. Plant, Soil, and Nutrition Laboratory
Hazard Communication--Your Right to Know
MSDS
Laboratory Safety
Practicing Safe Science
Chemical Hazards
Laboratory Hoods
Emergency Response
Selection and Safe Use of Personal Protection Equipment
Centrifugation, Chemical Storage, and Glassware Hazards
Radionuclide Hazards
USDA Laboratory Compliance with RCRA
Safe Use of Compressed Gases
Safe Use of Biological Safety Cabinets
Office Safety
Maintenance Safety
Electrical Lockout/Tagout
Laboratory Hoods
Mower Safety
Driving Safety
Working Safely with Solvents
USPSNL Hazard Communication Manual
USDA Radiation Safety Training Manual
Hazardous Waste Management Manual
Worker Protection Standard Training
USDA/ARS Radiation Safety TrainingAPPENDIX I
APPENDIX I
EMPLOYEE SAFETY CHECKLIST
USPSNL
ITHACA, NY
(Complete Appropriate Sections)