Page 10 |
![]() |
1 - Overview Of A Cotton Gin
2 - Page 3 3 - Page 4 4 - Page 5 5 - Page 8 6 - Page 6 7 - Page 7 8 - Page 9 9 - Page 10 10 - Page 1 |

Cotton ginning systems consist of several different types of processing machines and each is designed for specific tasks. Each machine influences several physical properties of the cotton fiber and many of those properties must be measured with complex laboratory instruments. The decision about the use of an individual machine involves a tradeoff, i.e. a cleaning machine will remove foreign material but also removes some valuable cotton and does some damage to the remaining fiber. A computerized process control system can optimize fiber quality by "prescription" processing the cotton.
Picture
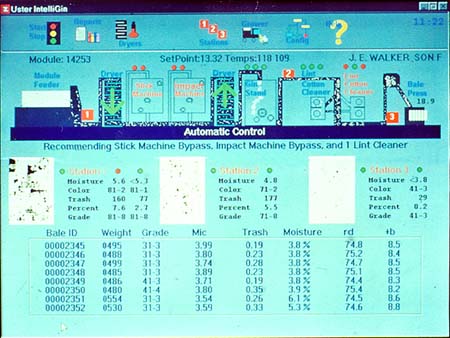
Process Control System
The first computerized process control system was installed in a small-scale research facility at Stoneville, MS, and used special routing valves to bypass or select any combination of four seed cotton cleaners, two multi-path driers, and three lint cleaners as directed by a computer. The current design uses three color/trash/moisture measurement stations in the gin system: in the feed control or module feeder, immediately behind the gin stand (before the lint cleaning), and after the lint cleaning. Station 1 evaluates seed cotton whereas stations 2 and 3 evaluate lint. The lint moisture, color, and trash measurements are used to predict the value of the cotton after treatment by all combinations of equipment which are available in the gin. Similar installations in six full-scale gins have also been evaluated.
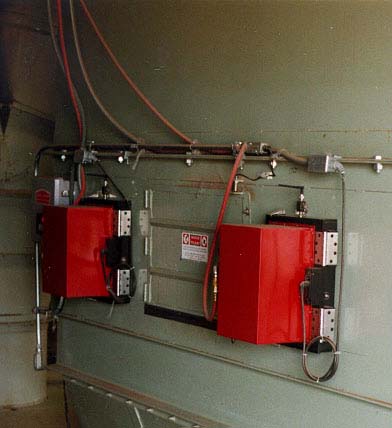
Station 1
Station 2
Station 3
Monetary Returns
Fiber Improvement by Process Control
Future
Gin Machinery Impact on Fiber Quality
Knowledge of the performance characteristics of gin machinery is the basis for controlling the gin process. W.S. Anthony developed the performance characteristics of each type of gin cleaning machinery and combination of machines in terms of their effect on fiber quality as a function of moisture and trash levels as well as cotton varieties. The study included three moisture levels (4.1, 5.5 and 8.4%), and three trash levels (3.0, 4.1 and 7.8%) based on the Shirley Analyzer visible foreign matter. Samples were taken before gin processing and at the feeder apron and lint slide to determine the characteristics of the seed cotton as well as the characteristics of the lint cotton. Foreign matter and moisture analyses were performed by the Cotton Testing Laboratory (CTL) at Stoneville. HVI and Smith-Doxey classifications were done by the Agricultural Marketing Service at Greenwood, MS. Neps, seed-coat fragments and short fiber content were determined at the CTL at Stoneville, MS. Foreign Matter
The visible and total foreign matter remaining in the ginned lint were a function of the variety, moisture, and machinery treatments. Visible lint foreign matter ranged from 3.9% to 6.2% as moisture increased, and from 2.0% to 7.4% as ginning machinery was changed. Length Measurements
Staple length ranged from 36.0 for the EFGS only to 35.1 for the 3-lint cleaner treatment. All lint cleaner treatments decreased staple length. HVI length corresponded directly with moisture level and was 1.10, 1.11 and 1.12 in. respectively, for the low (4.1%), medium (5.5%), and high (8.4%) moisture levels. No difference existed in length values for the seed cotton cleaners. However, each lint cleaner reduced the length by 0.01 in. Mean lengths, as measured by the Peyer 101, for machinery ranged from 0.86 in. for the three lint cleaner treatment to 0.92 in. for a treatment with no lint cleaners. Mean length decreased from 0.93 in. to 0.87 in. as lint moisture decreased from 8.4% to 4.1%. The short fiber content (fibers less than 0.5 in. in length) by weight increased from 4.6% to 8.7% as moisture decreased from 8.4% to 4.1%. Seed cotton cleaners did not increase the short fiber content but lint cleaners did. Lint cleaners increased the short fiber content to 6.8, 8.8 and 9.6%, respectively, as one, two and three stages of lint cleaning were used. Length Uniformity and Strength
The uniformity was higher for the high moisture level, 82.8, than for the medium, 82.2, and low, 81.9, moisture levels. The Machinery treatments caused the mean uniformity to vary from 81.4 (three lint cleaners) to 82.8 (extractor-feeder and gin stand (EFGS) only or stick machine with EFGS) with lint cleaners decreasing uniformity about 1.0. Strength means for moisture were 28.0, 28.6 and 29.2 g/tex, respectively, for cotton processed at 4.1, 5.5 and 8.4% fiber moisture. Seed-coat Fragments and Motes
The number of seed-coat fragments per 3 grams of lint were about 50% higher at the low moisture level than at the two higher levels. Machinery did not significantly influence the number of seed-coat fragments. The weight of seed-coat fragments was significantly influenced by Moisture and Machinery. Means for the high moisture level were significantly higher (33.8 fragments) than for the other two moistures (28.5 fragments). Machinery strongly influenced fragment weight with the seed cotton cleaners having no effect and lint cleaners decreasing the weight dramatically. The number and weight of motes were decreased dramatically by saw-type lint cleaners. Neps
Small entanglements of cotton fibers called neps increase each time that cotton is manipulated. G.J. Mangialardi studied samples of cotton fiber collected in seven locations in a gin system and found that neps were increased from 6 to 16 per 100 in.2 of web by simply removing cotton from the trailer pneumatically. Two stages of lint cleaning increased the number of neps dramatically from 18 to 34. W.S. Anthony reported that neps averaged 13.1 and 6.7 per 100 in.2 of web for lint moisture contents of 4.1% and 8.4%, respectively, a decrease of 49% across all machines. He also reported that neps decreased by 15% and 42%, respectively, when one and two stages of lint cleaning were bypassed.
<< Previous
1
2
3
4
5
6
7
8
[9]
10
Next >>
Foreign Matter
Length Measurements
Length Uniformity and Strength
Seed-coat Fragments and Motes
Neps
<< Previous 1 2 3 4 5 6 7 8 [9] 10 Next >> |